Call us on 01386 430 121

Essential Information
This page contains information that we think you should know if your thinking about buying a pre-cast concrete building;
Concrete Garages as an Alternative to Conventional Brick Construction

Since the total cost of a concrete garage is usually about one third of that for a comparable brick built structure, many homeowners have chosen the sectional concrete approach to enable them to save money and time. Erection time for sectional concrete is generally one day whereas brick construction which requires deep foundations, will mean a minimum of four to six weeks at best.
With the sectional garage, groundworks are cheaper, as the depth required for the footings is about a third of that required for brick construction (about a metre), and the earth removal costs, now running at about ninety pounds per skip (in part due to the new landfill tax), are drastically reduced.
As an additional bonus concrete garages can be extended very easily at a later date, with door and window arrangements changeable at any time. They can even be removed and re-sited elsewhere.
Garage Appearance

Where the exterior finish of the dwelling is rendered, our interlocking panels are the only type that can be rendered to match the existing house without the prospect of the seal between the panels opening up with time. All our panel garages feature the exclusive tongue-and-groove construction system originally developed by Marley.
Where the property is of brick construction, the front pillars either side of the garage door can be finished in mock brick. Most manufacturers provide only one finish. With Leofric/Mayfair there are six wall finishes available, including natural Cotswold and Mendip stone.
Today’s home buyer is well aware of appearance, or shall we say, “kerb appeal”. Estate agents have commented that a cheap looking garage can hold the price of a property down, whereas our Heritage Model with it’s side-to-side roof ridge, will add as much as three times it’s cost in many locations.
Fort Knox Doors

The ‘Premium Grade’ Fort Knox doors are outward opening ONLY
Construction Time

Conventional brick or block construction is affected by weather conditions and requires deep concrete foundations (usually about 1 metre in depth) which need to harden before any bricks are laid. Typically a conventionally-built double garage will take four to six weeks to complete.
You should also be aware that the builder that you select is required to notify the Health & Safety Executive (H&SE) of the project, if the construction time, including preparation of the site, extends beyond thirty days. As current legislation stands, you are not responsible for complying with H&SE requirements, but your builder is. If he fails to comply your project could be stopped. A competent, professional builder should have no problems in providing the local authority with all certifications presently required. These include matters such as First Aid, scaffolding tower erection, plant, especially for any engine-driven units, etc. However, anyone carrying out work without the correct training certifications, which today include even scaffolding, would be stopped. This could delay your project, or even necessitate the appointment of a new builder.
The Base

It is the responsibility of the customer to provide a good base. Usually our agent will arrange this for you. Please note that there is always the possibility that the garage erector may reject the base and not erect the garage. The manufacturer should provide a base plan. Purchasers of Leofric and Mayfair Garages are always supplied with such a plan, together with full details of the base specifications.
The base must be flat; with the exception of the outer edge which needs a roll-off profile to ensure that rainwater is drained away from the garage, not attracted into the building by an inward fall from the edge. It is important to remember that an uneven base may well be rejected by the erector if, in his judgement, the garage cannot be erected in a level and upright manner, or if he feels that rain will run back into the building. Although a fillet of sand and cement is provided, water laying up against the garage wall will eventually gain ingress and, with frost, will start to break the seal.
The Concrete

Making concrete is not unlike making a cake. The chief components of concrete are sand, of which there are many grades, cement, of which there are also many grades, and the aggregate of which there is a vast selection of sizes and types to choose from. All these components need to be carefully selected, and in the final analysis it is the hardness of the concrete that demonstrates the quality of the mix.
Local materials usually do not combine to make the best concrete, and it may well be necessary for manufacturers to purchase from a distant quarry, which has higher cost implications bearing in mind today’s increased transportation costs. Check with the garage manufacturer. The hardest material available is carboniferous limestone, which we use. The stone needs to be hard and sharp edged to bond properly. Aggregate coming from sandstone regions (sometimes called jurassic limestone) is not hard enough, and river stone is too rounded. When broken, concrete made with river or pit stone has the stone exposed, looking like the peanuts in a broken chocolate nut bar.
Ask the manufacturer to state the hardness/strength of their product. Leofric concrete reaches a hardness of 41KN per SqM after 35 days. That is almost twice as hard as some of our competition! It is also very important that the concrete be free of metal particles especially iron, which will gradually weep, causing a red rust stain to run down the panel. Avoid panels with the reinforcing rods showing through. With time the concrete will spall and flake off. Small surface fissures are acceptable, but cracks through the panel are not.
Reinforcing rods are vital. Most of our industry use smooth wire to benefit from lower cost. It can be bought in coils and straightened with a special machine. We have such a machine, but have changed over to a barley-twist type rod, which is dearer, and the material has to be bought in straight lengths, as it will not pass through the straightening machine. Also we use 8mm rod, not 6mm as is common with the competition.
Construction

There are two systems, the post and panel and the panel only versions.
The Post and Panel Garage

A post and panel building, whether a garage or shed, uses vertical posts at 4′ centres, with fill-in panels, each panel being about 2′ height. Different building lengths can be achieved with as many 4′ or 2′ add-on panels, as required. The panels usually fit to the posts with a tapered groove joint and a metal clip clamping the panel to the post.
If you wish to select a building of this type we suggest that you check the following:
1. Thickness of the Panel – Leofric is not less than 1.5″ at any point and over 2.5″ around the panel edge.
2. Steel Reinforcement of Panel – needed for strength. See previous comments.
3. Post Section Size – Leofric corner cross section is 4.5″ by 8″ and the interposts measure 5.5″ by 3.5″.
4. Steel Reinforcement of Post – Leofric posts are reinforced with 8mm knurled rods
5. Finishes Available – Leofric offer Rockwall, Shiplap, and stone covered panels in six finishes.
6. Can You Build it Yourself? – With Leofric you can. This will save several hundred pounds on a large garage.
The Panel Garage

Panel Garages do not require posts. Each panel has a thickened edge and panels are bolted or clipped together. In order to permit mass-production, all panels with the exception of those made by Leofric Building Systems are cast in fall-out moulds. The concrete panel has to be tapered around the outside edges so that turning the mould over will cause the panel to fall out. The Leofric (and Mayfair) Garage panels are derived from the Marley garage range which was acquired by Leofric in 1990. The edges of the Marley design are not tapered, instead the mould has four hinged sides that require manual release and fold down before the panel can be removed. The tongue and groove profile around the edge of the panel enables strong, weatherproof panel-to-panel joints, but prohibits the panel from falling out when the mould is inverted adding slightly to the manufacturing cost. Again there are many factors to be aware of:
1. Thickness of the Panel – Leofric/Mayfair panels are just under 2″ in the centre and about 4″ around the edge.
2. Steel Reinforcement of Panel – needed for strength. We use 8mm knurled bar, most competitors use 6mm smooth wire.
3. Finishes Available – We have five stone finishes available plus the advantage of rendering, not offered by any other company. Their butt-up panel construction, without a mechanical tongue-and-groove joint, cannot be rendered as it would soon show cracks between the panels.
4. Can you Build it Yourself? – With Leofric the answer is yes – and this could save several hundred pounds on a large garage. This option is not available with the majority of other brands.
The Roof

Garages are supplied with roofs made from a wide variety of materials. Choices can be made from corrugated metal, fibre cement or tiles. Metal sheets can be galvanised, which is the cheapest, painted or steel, plastic laminated. Fibre cement sheets are less likely to generate condensation, however they can be slightly porous and need a minimum slope angle to ensure that water runs off cleanly, otherwise they can saturate and seep. Tiling is available of some models and this could be metal formed tiles or genuine house roof tiles, such as those made by Marley, which are used exclusively in the Leofric and Mayfair Garage Ranges. The warranty period for the tiles needs to be noted. For Marley Tiles this is fifty years.
In some parts of the country there are Planning Restrictions that require that roofing must be in accordance with local requirements. Leofric can supply garages without roofs, thus where local slate or stone tiles are mandatory they can be fitted. However should this requirement affect you, be certain that the roof supports of the garage will carry this heavier load.
Check out the way in which the roof is supported. Leofric uses full roof trusses which sit on, or are bolted directly to, the concrete sections. Note how some companies (even the self-appointed “market leaders”) obtain the 7′ internal height that our garages provide by using a 6′ 6″ panel and a 6″ vertical metal strap to gain the extra 6″ needed to equal our construction. Also check the door closing mechanism. If wires are used to lock/unlock the door at several points, then just one wire stretching or breaking will render the door unopenable.
Guttering

Guttering is essential for garages that have a ridge roof running across the building, such as our Mayfair Heritage model, and it is provided on this garage so that water does not drip down your neck as you open the door. Some Leofric models are supplied without guttering, as it can, in certain circumstances, serve to concentrate water flow over the same section of the garage base, causing soil or plant erosion, unless proper drainage has been provided for when the base was laid.
Planning & Building Regulations

In most parts of the country, our concrete sectional garages and sheds do not require Planning Consent Approval, whereas any brick structure will certainly be subject to Building Regulations. Our Sales Agents can advise you on your local requirements and assist you with any documentation if this is required. If Planning Consent is required Leofric will provide, free of charge, a set of plan and elevation drawings for any model of our range of garages.
If the proposed garage is not going to project in front of the existing property, planning permission is not normally required, providing the garage is within certain size limits which, in turn, are governed by the size and other aspects of the existing building. Normally you do not need Planning Consent to erect a garage of less than 30 square metres (322 square feet) floor area.
We hope that we have given you an insight into the world of sectional concrete buildings. The range of products on the market may look very similar but, as you will have read here, there are important differences. A well-styled garage that blends with your property will add value greater than the direct cost. A Mayfair Heritage will usually add twice it’s purchase price to the overall property value, or even more depending upon location. Steer clear of cheap-looking models. In today’s property market they can have a negative effect on your property value.
Security

Only Leofric and Mayfair Garages employ a “tongue and groove” coupling detail between wall panels. All other manufacturers use panels that just butt-up. Apart from the weaker construction aspect of their approach this also permits a hacksaw blade or similar instrument to be forced between their panels enabling the two bolts (as used by Compton) to be cut through and the wall panels forced apart. No blade can be forced between Leofric/Mayfair wall panels and there are seven coupling bolt holes available if required.
Our post and panel garages can be fitted with anchor bolts in the posts so that no bolt head can be sawn off. This addition to our normal specification carries a slight extra cost.

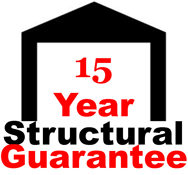